Common Mistakes in Freight Documentation and How to Avoid Them
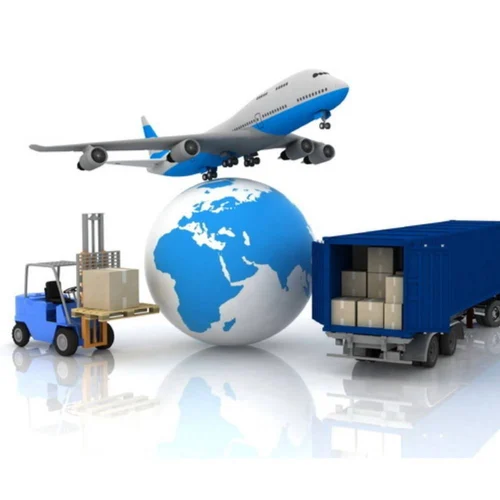
Freight documentation may not be the most exciting part of the shipping process, but it’s one of the most crucial. A missing detail or typo can lead to costly delays, rejected shipments, fines, or lost cargo.
Whether you’re an experienced exporter or just getting started with logistics, mistakes in freight documents are more common than you might think. The good news? Most of them are preventable.
In this article, we’ll walk you through some of the most common freight documentation errors and show you how to avoid them — all in plain, easy-to-follow language.
Inaccurate or Incomplete Information
One of freight documentation’s biggest and most frequent mistakes is entering incorrect or incomplete data. This could be:
- A typo in the consignee’s name or address
- Incorrect product descriptions
- Mismatched weights or quantities
- Missing HS codes or product classifications
Why it matters:
Customs authorities rely on these documents to clear goods. Inaccurate information can trigger red flags, leading to delays, extra inspections, or denied entry.
How to avoid it:
Always double-check entries, and ensure all details — including names, addresses, invoice values, and descriptions — match all related documents.
Misuse or Misunderstanding of Freight Terms
Terms like FOB (Free on Board), CIF (Cost, Insurance & Freight), and EXW (Ex Works) define who is responsible for what, including costs, insurance, and risk.
Common error:
Using these terms without fully understanding their implications, or applying them inconsistently across documents.
How to avoid it:
Ensure your trading partners agree on Incoterms (International Commercial Terms) upfront. If you’re unsure about the meaning, it’s worth getting clarification from a freight forwarder or logistics expert.
Missing or Incorrect Signatures
Several freight documents require signatures to be valid, such as the Bill of Lading, commercial invoice, and export declaration forms.
Why it matters:
Customs or carriers may not accept unsigned or incorrectly signed documents. This can hold up your shipment or cause legal complications.
How to avoid it:
Identify who is responsible for signing each document. In many companies, it’s someone from logistics, finance, or the shipping department. Set up a document checklist to ensure nothing gets missed.
Incorrect Packaging and Labeling Information
The packing list and labels on your goods must match the documentation exactly.
Common errors include:
- Incorrect number of packages listed
- Wrong dimensions or weights
- Mismatched package numbers between documents and boxes
How to avoid it:
Coordinate closely with your warehouse or packing team. Review the final packing list and labels before generating or sending documents to your freight partner or customs agent.
Overlooking Country-Specific Requirements
Different countries may have unique document requirements, import restrictions, or formatting rules.
Why it matters:
Sending documents that don’t meet a country’s legal or regulatory standards can result in cargo being detained or rejected.
How to avoid it:
Work with a freight forwarder or customs broker who understands the specific requirements for the destination country. They can help ensure compliance with local laws and avoid costly surprises.
Confusing or Inconsistent Use of Freight Documents
Many types of freight documents are involved in international shipping, including the bill of lading, commercial invoice, packing list, certificate of origin, andconsignment note.
What goes wrong:
People sometimes mix up these documents or use the wrong one at the wrong stage of the shipment. For example, treating a consignment note as proof of ownership, which it’s not, or providing a commercial invoice without the required HS codes.
How to avoid it:
Train your staff on the purpose of each document. Use templates for consistency, and maintain clear document checklists for each shipment.
Failure to Update or Match Digital Records
As more logistics systems go digital, syncing paper documents with electronic records is becoming a critical step.
Common issues:
- Manual entries that don’t match the digital system
- Failure to upload the required documents to the carrier or customs portals
- Mismatched shipment numbers or invoice references
How to avoid it:
Use centralized logistics software like ERP software, which integrates with your freight and inventory systems. Regular audits can also catch errors before they create real problems.
Ignoring Insurance Documentation
Not providing the right insurance paperwork can leave you exposed if anything goes wrong during transit, like damage, theft, or loss.
Common mistake:
Failing to include the insurance certificate, or providing incorrect coverage details.
How to avoid it:
Always confirm that the type of insurance, value of the goods, and shipping route are correctly documented. Include a copy of the insurance certificate in your freight documentation package.
Poor Communication Between Teams
Sometimes, it’s not about a specific document but the lack of coordination between departments.
For example:
The sales team promises next-day delivery, but the logistics team isn’t informed in time to process the documents, leading to a delay.
How to avoid it:
Create a clear internal workflow that includes everyone involved — from sales to warehouse to finance. Use shared platforms or dashboards where updates can be tracked in real time.
Final Thoughts
Freight documentation mistakes can be frustrating, expensive, and damaging to customer relationships — but they’re also highly avoidable. By taking a proactive approach, using checklists, verifying details, and leaning on experienced logistics partners, you can significantly reduce the risk of errors.
Understanding documents like what is consignment note, the bill of lading, and the commercial invoice can go a long way in making your shipping process more efficient and professional.
In logistics, details matter — and everything else runs much smoother when you get them right.